ICFPro.ca is a division of ICFhome.ca - Phone 1 866 868-6606 - Direct Line 1 705 533-1633 - Email: info@icfhome.ca
Fire-Resistant Homes
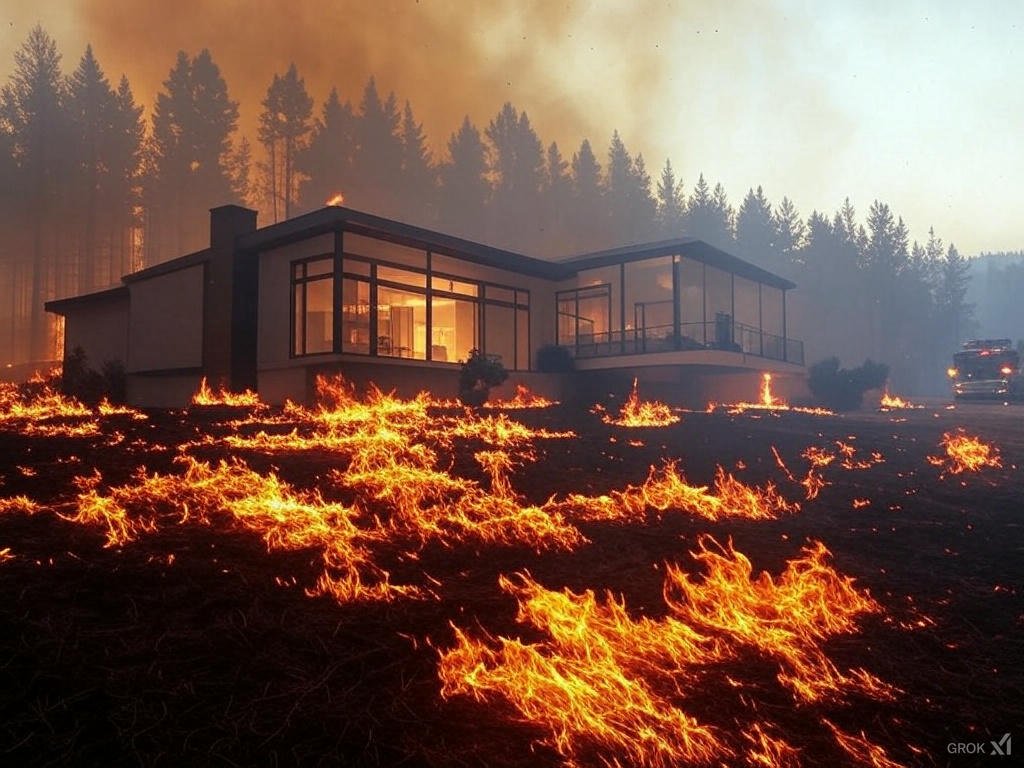
Fire-Resistant Homes: How Insulated Concrete Forms (ICFs) Lead the Way in Safety and Efficiency
In an era where wildfires are becoming more frequent and intense, the demand for fire-resistant homes has never been more pressing. Homeowners in fire-prone regions are increasingly seeking construction methods that offer superior protection without compromising comfort and energy efficiency. One solution stands out: Insulated Concrete Forms (ICFs).
ICFs have gained significant attention for their resilience against fire, energy efficiency, and long-term durability. Backed by scientific testing, real-world case studies, and cost-benefit analyses, ICFs are revolutionizing the way homes are built for safety. This comprehensive guide explores why ICFs are the gold standard for building fire-resistant homes.
🔍 What Makes a Home Truly Fire-Resistant?
To understand why ICFs excel, it’s essential to grasp what makes a home resistant to fire. Fire-resistant homes are designed and constructed using non-combustible materials, tight construction methods, and fire-rated assemblies that can withstand high temperatures without structural failure.
Key factors include:
- Material Composition: Walls, roofs, and insulation made from non-combustible or fire-retardant materials.
- Thermal Resistance: Walls that slow heat transfer, preventing interior ignition.
- Structural Integrity: Assemblies that maintain load-bearing capacity during prolonged fire exposure.
- Flame Spread and Smoke Generation: Low flame spread ratings and minimal smoke production.
ICFs check all these boxes, offering homeowners peace of mind in fire-prone areas.
🧬 Why ICFs Are the Gold Standard for Fire-Resistant Homes
1. Superior Material Composition
ICFs consist of two layers of expanded polystyrene (EPS) foam filled with reinforced concrete. Each component plays a crucial role in fire resistance:
- Concrete: Non-combustible with a melting point above 3,000°F—far higher than the temperatures reached in most residential fires.
- Polystyrene Foam: Treated with fire-retardant chemicals, such as Hexabromocyclododecane (HBCD). While the foam melts under extreme heat, it does not ignite or contribute to flame spread.
2. Fire Resistance Testing: How ICFs Perform Under Heat
The fire resistance of building materials is typically evaluated using the ASTM E119 standard, which exposes wall assemblies to continuous heat and flame until structural failure or fire penetration occurs.
ICF vs. Traditional Wood Frame:
Feature | Wood Frame Home | ICF Home |
---|---|---|
Fire Endurance Time | 45–60 minutes | 4 hours+ |
Temperature Resistance | Up to 1,100°F | 2,000°F+ |
Structural Integrity | Collapses quickly | Maintains structure |
According to a study by the Portland Cement Association (PCA), ICF walls withstood 2,000°F heat for 4 continuous hours without failure. In contrast, wood-framed homes typically collapse within an hour under similar conditions.
Graph: Fire Resistance Comparison – ICF vs. Wood Frame
🌡️ Thermal Performance: Slowing Heat Transfer
One of ICF’s standout features is its high thermal mass, which slows heat transfer and prevents flames from reaching interior spaces. The ICF Manufacturers Association (ICFMA) conducted a comparative study in 2016:
Wall Type | R-Value (Thermal Resistance) |
Wood Frame | 15 |
ICF Wall | 22 to 30 |
ICFs offer up to 58% better thermal resistance than wood-framed walls, making it harder for heat to penetrate the structure.
Graph: Comparative R-Values – ICF vs. Traditional Materials
🚫 Flame Spread and Smoke Development
The ability of a material to resist flame spread and minimize smoke generation is critical for fire safety. This is measured using the ASTM E84 standard, which assigns a Flame Spread Index (FSI) and a Smoke Developed Index (SDI).
Feature | ICF Foam | Wood Frame |
Flame Spread Index (FSI) | Less than 25 | Over 200 |
Smoke Developed Index (SDI) | Around 450 | Exceeds 450 |
ICF foam is classified as a Class A material, meaning it has the highest possible resistance to flame spread.
Graph: Flame Spread and Smoke Development – ICF vs. Wood
🏚️ Real-World Proof: ICF Homes That Survived Wildfires
The Camp Fire, California (2018)
The Camp Fire was one of the deadliest and most destructive wildfires in California history, reaching temperatures of 1,472°F and destroying over 18,800 structures.
Amid the devastation, one home built with Logix ICF blocks in Paradise, California, remained standing. This home had:
- 6-inch ICF walls with a 3-hour fire rating.
- Fire-resistant windows and roofing.
- Minimal damage, while surrounding wood-framed homes were reduced to ash.
“ICF saved our home. The walls endured intense heat while the fire raged around us.” – Paradise homeowner.
💰 Energy Efficiency and Cost Implications
While fire resistance is the primary advantage, ICF homes also excel in energy efficiency and long-term cost savings.
1. Energy Savings
A study by the Oak Ridge National Laboratory (ORNL) found that ICF homes can reduce heating and cooling costs by up to 20%, depending on the climate zone. In hot climates like Phoenix, the savings were even more pronounced.
Feature | Wood Frame Home | ICF Home |
Energy Savings | Baseline | Up to 20% |
HVAC Size Reduction | Standard | 30% smaller |
2. Construction and Insurance Costs
ICF construction costs slightly more upfront but offers significant long-term savings:
Feature | Wood Frame | ICF Home |
Initial Construction Cost | $140/sq. ft. | $150/sq. ft. |
Insurance Savings | Standard | Up to 30% off |
Energy Savings (Annual) | – | $800–$1,200 |
Graph: Cost-Benefit Analysis Over Time – ICF vs. Wood
🌿 Environmental Impact and Sustainability
While concrete has a relatively high embodied carbon, ICF homes offset this through superior energy efficiency and long lifespan.
Key Sustainability Benefits:
- Longevity: ICF homes last 100 years+, reducing resource consumption over time.
- Reduced Waste: On-site construction generates less material waste.
- Energy Efficiency: Lower energy consumption reduces the home’s carbon footprint.
Emerging innovations, like bio-based foams and carbon-neutral concrete, are making ICF even more sustainable.
🚧 Challenges and Future Innovations
Despite their many benefits, ICFs are not without challenges:
- Higher Initial Cost: ICF homes can cost 5% to 10% more upfront.
- Specialized Labor: Builders must be trained in ICF construction.
- Material Availability: In some regions, sourcing ICF blocks may require pre-ordering.
However, advancements in recycled materials, sustainable foams, and standardized building codes are addressing these challenges.
🏆 Conclusion: A Safer, Smarter Way to Build
The evidence is clear: Insulated Concrete Forms (ICFs) offer unmatched protection for fire-resistant homes. From superior thermal performance to real-world survival stories, ICFs prove their worth time and time again.
- 4-hour fire resistance under extreme heat.
- 58% better thermal performance than wood framing.
- Up to 30% lower insurance premiums.
- Energy savings of 10% to 20% annually.
For homeowners in fire-prone regions—or anyone seeking peace of mind—ICFs are not just an option but a necessity. As wildfires intensify and building codes evolve, the future of safe, resilient housing lies in innovative solutions like ICF.
👉 Ready to build a fire-resistant home? Contact us today to learn how ICFs can protect your investment and your family.
Sources: Portland Cement Association (PCA), ICF Manufacturers Association (ICFMA), Oak Ridge National Laboratory (ORNL), ASTM International.