ICFPro.ca is a division of ICFhome.ca - Phone 1 866 868-6606 - Direct Line 1 705 533-1633 - Email: info@icfhome.ca
ICF Wall Systems
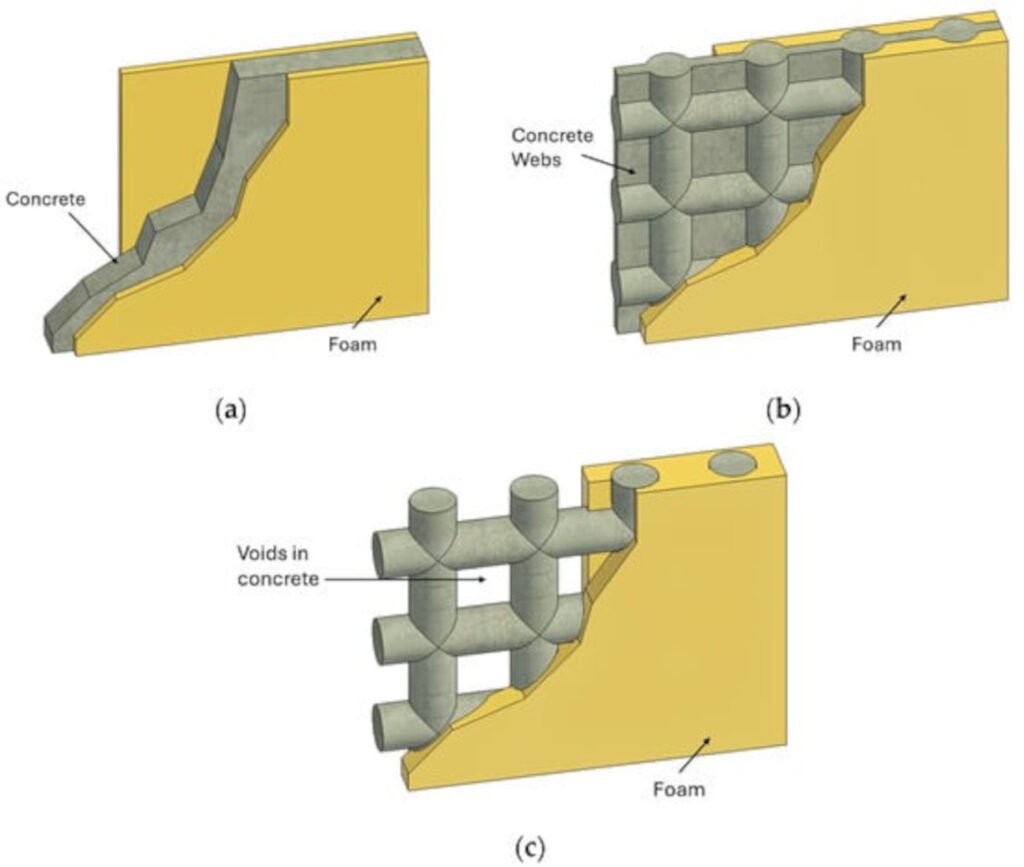
ICF Wall Systems Unveiled: Building the Future, One Foam Block at a Time
Imagine living in a home that’s as sturdy as a medieval castle, as quiet as a library, and as energy-efficient as a Tesla. Welcome to the world of Insulated Concrete Form (ICF) construction—a game-changing method that’s rewriting the rules of modern building. Whether you’re battling -30°C winters, hurricane-force winds, or just your neighbor’s leaf blower, ICF walls offer a fortress-like solution. But with three distinct systems to choose from, how do you pick the right one? Let’s break it down, brick by foam block.
The Three Tribes of ICF: Flat, Grid, and Post & Beam
1. Flat Wall System: The Heavyweight Champion
Structure: Picture a concrete sandwich—two layers of EPS foam (think thick Styrofoam) with a solid concrete core.
- Pros:
- Energy Efficiency: R-values up to R-26—like wrapping your home in a down-filled parka.
- Strength: Handles multi-story builds and 250+ mph winds (take that, hurricanes).
- Fire Resistance: Withstands flames for 4+ hours—longer than most fire departments’ response time.
- Cons:
- Cost: Uses 30% more concrete than other systems.
- Thickness: 12-inch walls steal 5% of your floor space.
Best For: Arctic climates, coastal storm zones, and anyone who wants a “forever home.”
Real-World Example: A cottage in Ontario’s Muskoka region slashed heating bills to $80/month despite -40°C winters.
2. Grid (Waffle) System: The Middle Ground Maverick
Structure: A ribbed concrete core—like a waffle—nestled between EPS panels.
- Pros:
- Material Savings: 20% less concrete than flat walls.
- Seismic Resilience: The grid pattern laughs at earthquakes (California-approved).
- Cons:
- Thermal Bridging: Concrete ribs can create sneaky cold spots.
- Labor Intensity: Precision bracing required—no room for “good enough.”
Best For: Earthquake zones, eco-warriors cutting carbon footprints.
Case Study: A San Francisco retrofit survived a 7.1 quake without a crack.
3. Post & Beam System: The Architect’s Playground
Structure: Vertical ICF columns and horizontal beams, with insulated panels filling the gaps.
- Pros:
- Design Freedom: Create soaring glass walls or cantilevered decks.
- Concrete Diet: Uses 40% less concrete than flat walls.
- Cons:
- Engineering Puzzles: Requires a structural engineer’s seal of approval.
- Air Leaks: More joints = more potential gaps.
Best For: Modern designs, commercial spaces, and Frank Lloyd Wright wannabes.
Showstopper: A Colorado mountain retreat features 20-foot glass walls framed by ICF posts.
Building with ICF: A Step-by-Step Survival Guide
- Foundation First:
- Opt for frost-protected shallow footings in cold climates—they’re cheaper and code-approved.
- Stack ‘Em High:
- Interlock EPS blocks like LEGO bricks, using plastic ties to keep them aligned.
- Rebar Jungle:
- Weave steel rebar vertically and horizontally—think of it as your home’s skeleton.
- Concrete Tsunami:
- Pump concrete into the forms in 4-foot “lifts,” vibrating out air bubbles like a bartender shaking a cocktail.
- Curing Magic:
- Let the foam trap moisture, curing concrete slowly for maximum strength.
Pro Tip: Hire an ICF-savvy crew. Mistakes here are not DIY-friendly.
The Hidden Battles: Moisture, Wires, and Inspectors
- Moisture Menace:
- Problem: Groundwater wicking into concrete.
- Fix: Install footing drains and capillary breaks (a 500solutionvs.500solutionvs.10k repairs).
- Electrical Quirks:
- Problem: Hitting rebar while drilling for outlets.
- Fix: Use a metal detector and pre-installed PVC conduits.
- Inspector Intel:
- Problem: “ICF? Isn’t that a rapper?”
- Fix: Bring ICC reports and cookies. Bribery works.
Cost vs. Value: The 5–10% Premium That Pays Dividends
- Upfront Cost: ICF adds 15–15–25/sq.ft vs. wood’s 10–10–15.
- Long-Term ROI:
- Energy Savings: 1,500–1,500–3,000/year (hello, early retirement).
- Insurance Discounts: 5–20% off premiums for disaster-proofing.
- Resale Boost: Homes sell 5–15% faster and for more.
Math Check: A $1M Toronto home recoups the ICF premium in 7–15 years. After that? Pure profit.
The Future of ICF: Smarter, Greener, Stronger
- 3D-Printed Forms: Custom shapes with zero waste—coming to a job site near you.
- Phase-Change Insulation: Wax-infused EPS that melts to cool and solidifies to warm.
- Carbon-Neutral Concrete: Slashing emissions without sacrificing strength.
FAQs: Burning Questions, No Fluff Answers
- “Can I hang a TV on ICF walls?”
- Yes—use concrete anchors or hit the foam’s fastener strips.
- “Will ICF work with radiant floor heating?”
- Absolutely. Embed PEX tubing in the slab pre-pour.
- “What about termites?”
- They’ll starve. Foam isn’t food, and concrete isn’t edible.
Conclusion: Why Settle for Ordinary Walls?
ICF isn’t just construction—it’s a legacy. Sure, it costs 5–10% more upfront, but what’s the price of sleeping through a storm, slashing energy bills, and knowing your home will outlive your grandkids? Whether you choose the brute strength of flat walls, the savvy efficiency of grids, or the open-concept freedom of post and beam, ICF is the ultimate middle finger to drafts, noise, and Mother Nature’s worst.
So, next time someone calls your ICF home a “foam box,” smile. You’ll be the one laughing when their wood-frame house creaks, cracks, and costs a fortune to heat.
Final Word: Building with ICF is like marrying a superhero—expensive upfront, but unbeatable in a crisis. 🦸♂️🏠